Last week Civic Engineers kindly hosted a site walk to allow others in the industry to see what’s happening behind the scaffold at 318 Oxford Street, the former House of Fraser building (future name “The Elephant“).
It was a fantastic opportunity to see the major surgery going on behind the scaffold! Thanks also to main contractor, McLaren Construction, and architect, Studio PDP, who helped with the tour and answered our (many) questions.
The building is stripped back with the structural alterations nearing completion. The overall contract is £132m, with Practical Completion due in Q4 2025. Development works are transforming the 250,000sqft former department store into an office-led mixed-use building, including 163,000sqft of commercial office, roof top restaurants, ground floor retail (facing Oxford Street) and a high-end gym.
With Civic Engineers on the project, it’s no surprise that retrofit, reuse and circular economy has been at the heart of the design. Simon Bennett has been working on the project for years and I was lucky to be on the tour with him where we heard about the design process and some key decisions.
One of the first challenges was to decide on massing and amount of retention. Simon and team optimised the reuse of existing structure, only removing some very compromised bays of structure on the east elevation and the compromised 6th floor. In a classic developer move, two additional floors are being added (so three floors of new construction) with step backs - all carefully calculated to balance extra massing/value whilst not requiring column strengthening beneath.
The Civic Engineers team spent a lot of time researching the existing building, painstakingly reviewing old photographs which revealed all sorts of details about how it was originally constructed. It gave away details of the steel frame, which is rather unique and a function of 1) the era of construction and 2) the fabricator, who was pioneering solid (yes solid) circular columns, apparently to maximise NIA - it’s good to know some basic economics haven’t changed!
Through detailed surveys and testing, any steel that wasn’t being retained in-situ, was reviewed for use again within the project or for potential to be of use elsewhere. 6t of columns were deconstructed and have been reused in the new frame on the upper floors. Then through a chance meeting while on a bike ride - an excellent justification for such events! - the beginnings of a deal was struck where 20t of structural steel would be deconstructed and re-fabricated for another project (different client, different engineers, different contractors - a true marketplace exchange). I actually visited the site where the steel ended up recently, so look out for a piece on the Tower Bridge Court (TBC) project in the future.
Another clever piece of engineering saw changes to the stability system, which unlocked extra bays of structure and allowed new services and circulation cores to be built into a more optimum layout. For stability, one new ‘core’ was created within the steel frame by adding some pretty chunky bracing. This is why you’ll note the lift shafts below are also sat within a steel frame with no concrete walls in sight.
Part of the ground and first floors, plus and a large part of the basement is going to be a gym, which must have a large pool. The structural zone for this has been brilliantly squeezed in-between existing columns and avoids their foundations, offering the tenant maximum potential for when they install the pool as part of their fit-out.
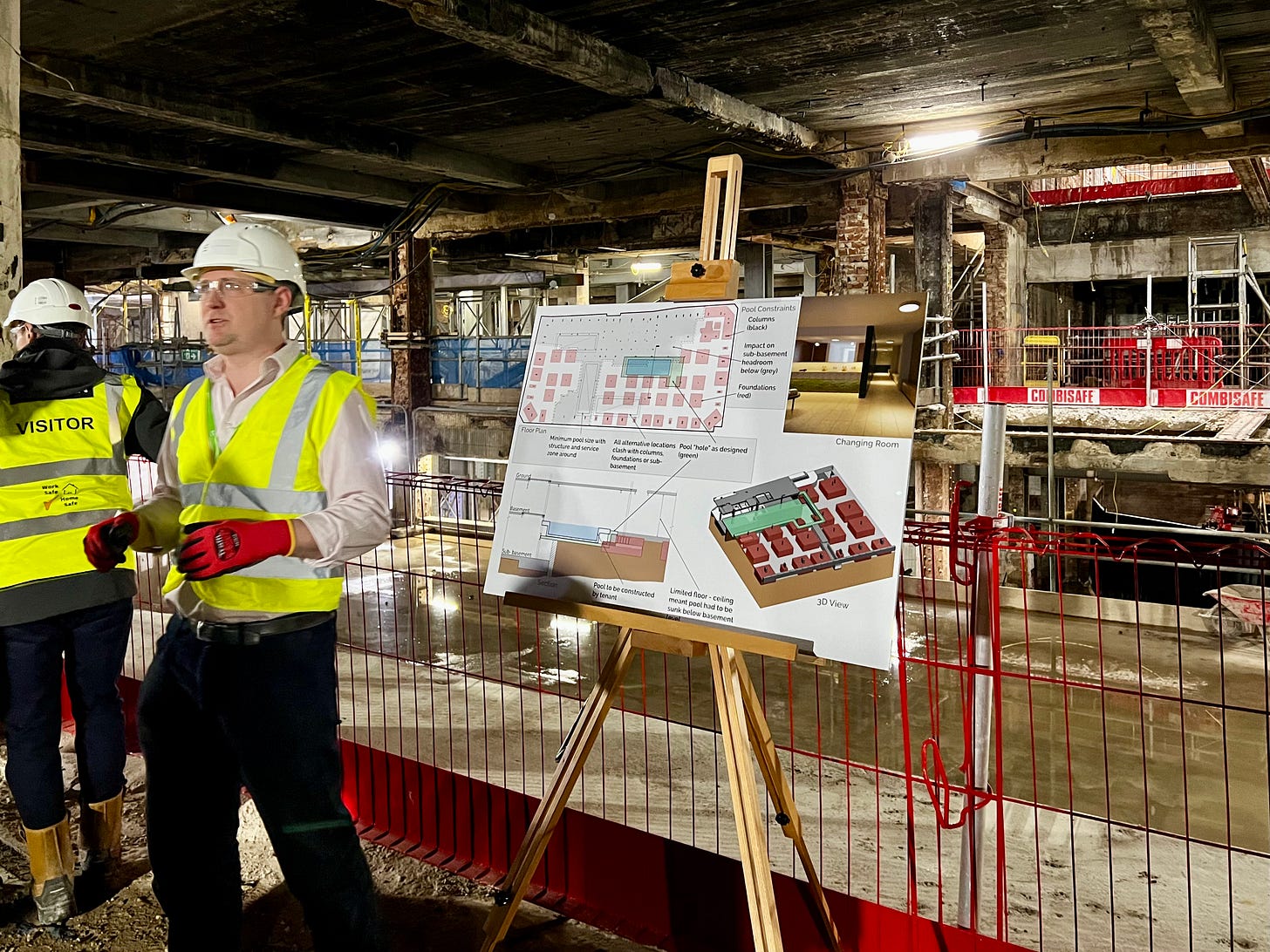
It goes to show that you shouldn’t always take things at face value, because this building had been reported to suffer from Regent Street disease1, however Civic Engineers took another, more detailed, look and found that hairline cracking was induced by notch details in the back of the stones, rather than corrosion of the steel frame. In fact, they found the steel frame was in remarkably good condition. All in all, this saved the project millions of costly facade repairs.
It slightly amused me to hear the structural engineer on the project explaining the office reception area (no offense Simon!). The aesthetic is very much client-led, with hard, high-end finishes including a lot of Portland stone. Detailing nods to features of the existing building and overall has an art-deco feel to it. I look forward to coming back in 18 months to see how it turns out.
What a brilliant tour and thank you again to Civic Engineers and the wider project team for facilitating a visit to a live construction site - no mean feat!
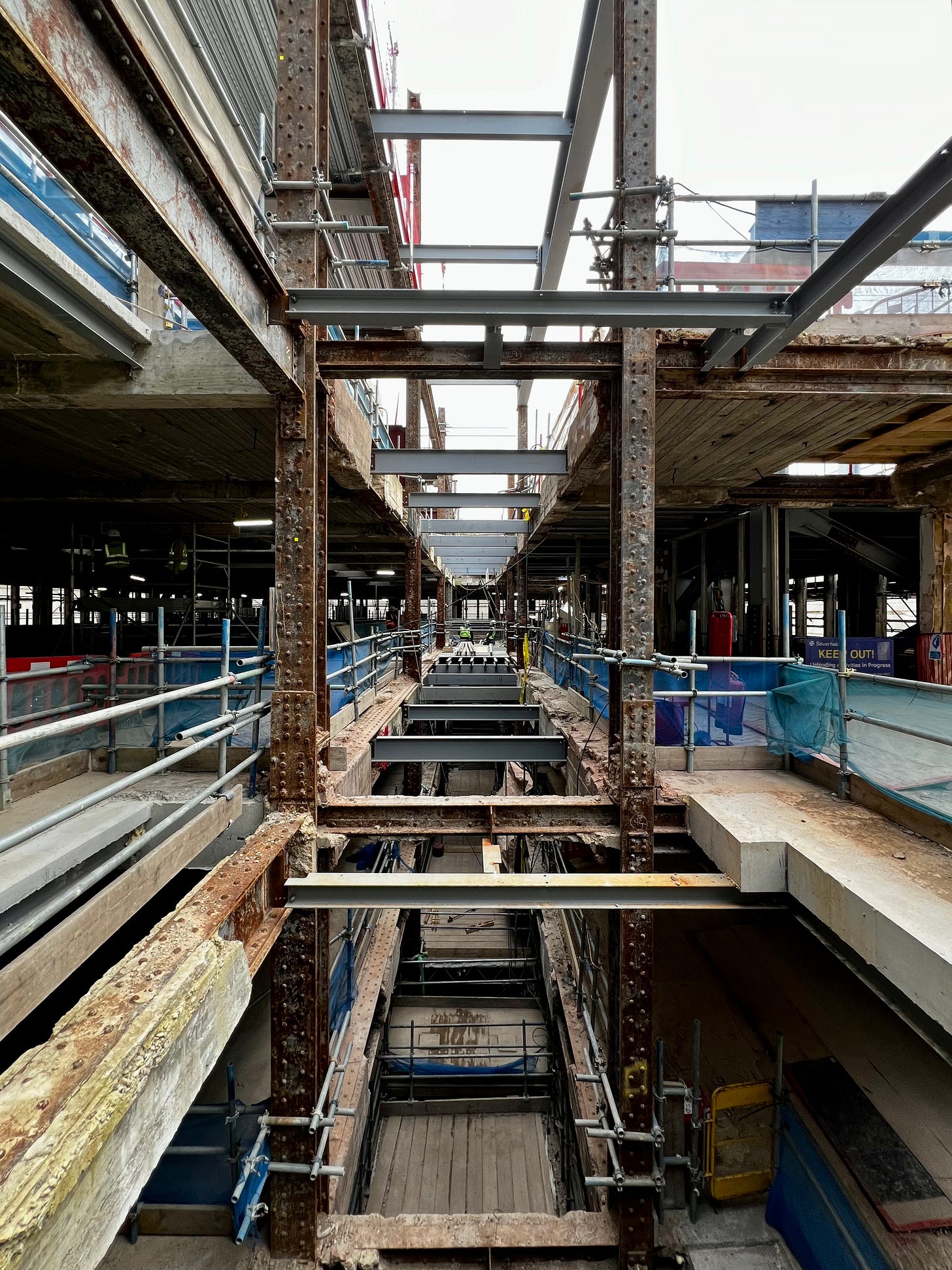
Regent Street Disease is the name given to the corrosion related damage that occurs in some buildings constructed during the first half of the 20th century using a steel frame embedded within the facing stone – in the case of Regent Street, Portland stone – but also in other materials such as brick or terracotta. Up to the 1950s construction of these buildings involved the tight packing of masonry or stone around the frame. Problems arise when the steel corrodes and causes a secondary effect, cracking of stonework around the steel frame.